19
Aug
Gas Assisted Injection Moulding
Gas assisted injection moulding a specific type of injection moulding that is a popular choice for manufacturing high performance plastic parts. The benefits of gas assisted injection moulding include the fact that it can increase tool life and produce higher quality parts.
What is the principle of gas assisted injection moulding?
Gas assisted injection moulding works by injecting pressurised nitrogen gas into the interior of a mould, forcing the molten plastic material against the outer surfaces of the mould. Gas can be simply used to ensure constant contact of the molten plastic against the tool whilst cooling to produce better looking parts, or be used to fill the core of the plastic and also improve its mechanical properties.
The gas assisted injection moulding process:
- Plastic polymer powder or granules are fed into the machine and heated.
- The molten polymer is then injected into the mould.
- Nitrogen gas enters the chamber and pressurises the molten plastic into the sides of the mould.
- The gas is released once the polymer cools after being held against the sides of the mould.
There are two types of gas injection moulding; external and internal.
Read more: Process of Injection MouldingExternal gas injection moulding
With external gas injection moulding, the molten resin is injected into the mould, before a thin layer of gas is injected into one side of the tool, usually the core. This forces the molten plastic against the cavity side of the mould. The gas applies pressure on the plastic as it cools, allowing the plastic to replicate the subtle details of the mould. External gas injection moulding is widely used when the design requires one side of the moulded part to have highly defined features or textured surface finish. However, the trade off is that surfaces in contact with the gas will have little to no surface texture.
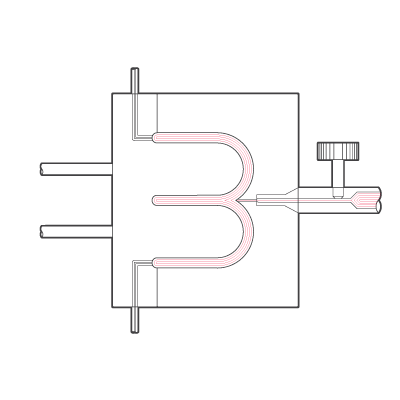
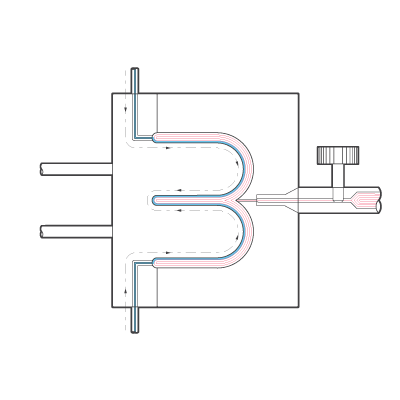
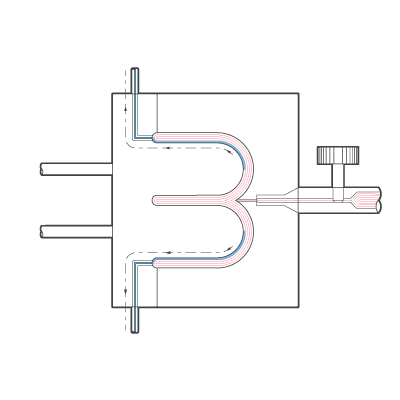